Sample Laboratory
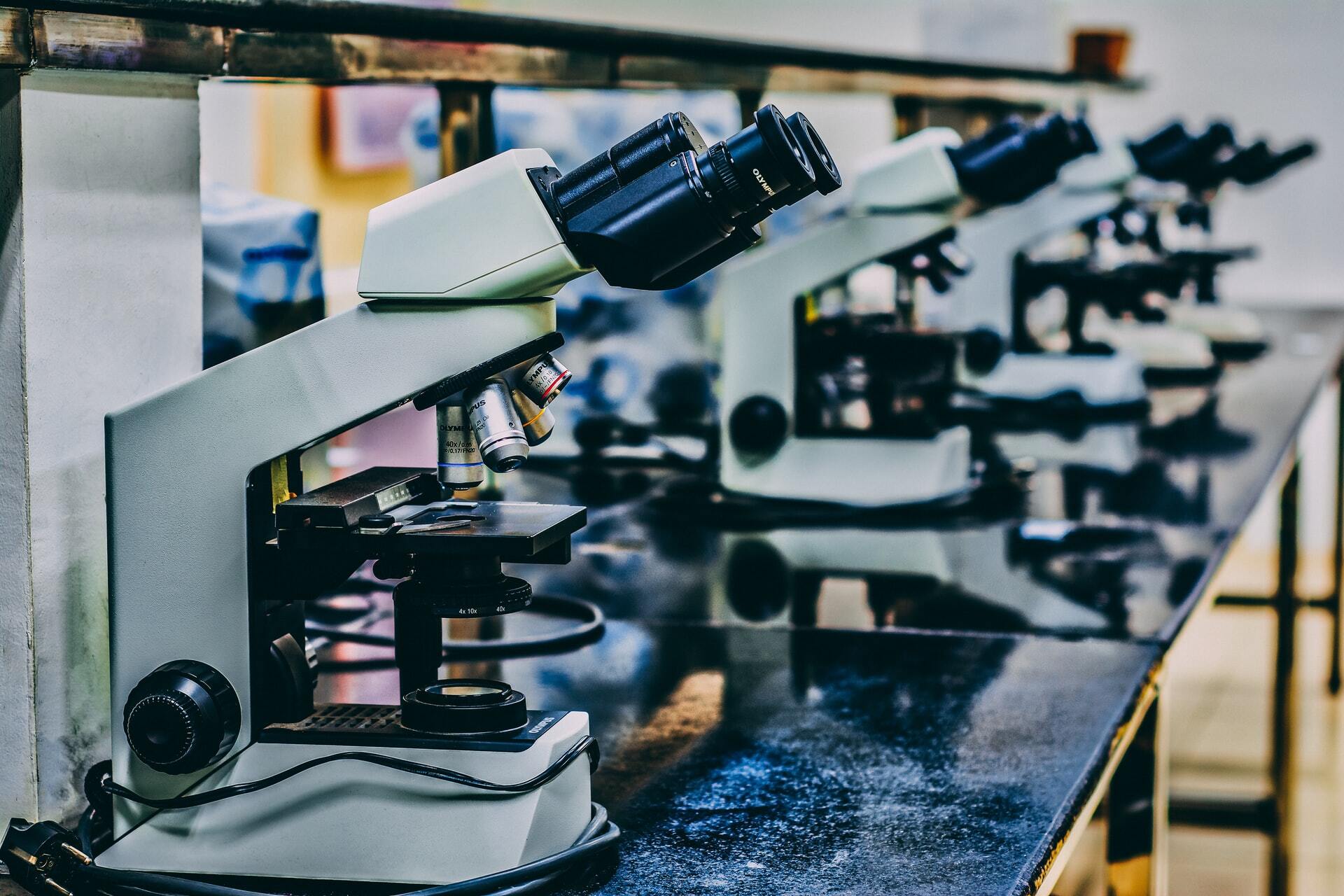
1.
Situation
The sample laboratory of this case is required by law to monitor their shipment temperature. Every container contains a tissue sample from a raw food ingredient. Upon receival the laboratory has to fill a form that includes information on the item, from the time of the taking of the sample and the shipping time to specifics about location and other details. Occasionally the same laboratory organization tests samples from humans as well, including blood and tissue samples.
The samples are obviously unusable if they arrive after going through incorrect conditions, which include too low and high temperatures. Because of this, the laboratory not only fulfils their responsibility for monitoring but also saves time by not testing samples that do not fit the set requirements. Since the operations occur on a daily basis, the monitoring solution used needs to be affordable and fast.
2.
Solution
When the organization receives a sample container, they scan a Logmore QR tag included in it. Since the sending process of every shipment needs to be efficient and fast to ensure the correct conditions, the organization has opted to not create missions or scan tags upon the sending, but instead use the missions feature retroactively by creating a mission for the shipping time upon receiving the container.
The sender places a Logmore QR tag into a thermal box along with the samples, seals it and fills the necessary paperwork for the recipient. As the shipment arrives at the sample laboratory, the laboratory employee opens the thermal box, retrieves the logger and creates the mission for the duration of the shipping process, ending it instantly. Thanks to the alert settings, they get instant notifications if any threshold-breaking temperatures have occurred.
To use the missions feature retroactively, the recipient opens Logmore Web, scans the QR tag and creates a mission for it. The starting and ending times for the mission are retrieved from the official paperwork that accompanies the thermal box. If anything that fits the alert parameters set by the organization has happened, the alerts are triggered without a delay and the employee sees the complete reporting for the shipping process effortlessly. Since it is a waste of time and resources to test a potentially spoilt sample, the employee saves those resources for that sample.
3.
Results
The laboratories now save on time and work, both through the time spent on work but also the laboratory resources. According to the laboratory representative, they cannot expect the sample senders to scan the QR tag, much less set up more complicated monitoring systems. Because of this, the QR tags and the retroactive missions were the perfect fit to the sample laboratory organization's stakeholder monitoring processes.
While the use case is not exceptional in how the QR tags are used, the way the organization has chosen to use the Logmore Web to maximize the benefit they get out of it is. By marking the QR tags associated with their account with distinct markings, they have also managed to boost the return-rate of the tags. By keeping track where each tag is sent, the organization knows exactly which stakeholder has one and which one has already sent theirs back for reuse along with shipments.