What A Strong Safety Culture Means To Your Company
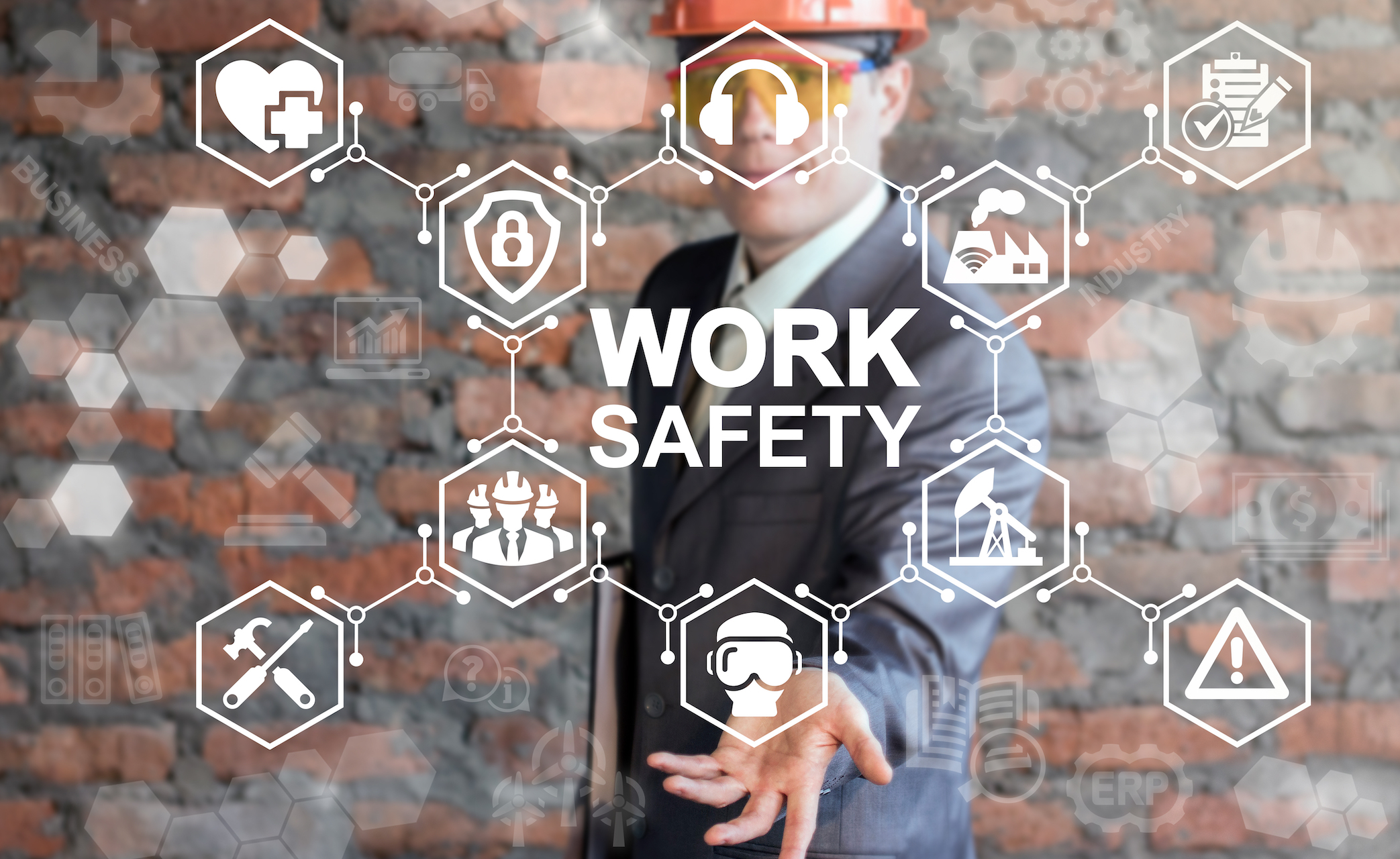
Including safety in your new employee training procedures and hanging up signs as reminders around the workplace aren’t impactful enough. Rather, the most effective approach is to instill a strong safety culture in your company.
Having a prominent culture of safety permeating every aspect of your company will not only serve to reduce the risk of myriad dangers, but it will also cause your employees to care about safety as much as you do, increasing your reliability and improving your reputation as a company. Embrace and reinforce a strong safety culture at your company.
Occupational safety
A concern for companies in all fields, the food and pharma industries pose specific occupational risks to employees as they are exposed on a daily basis to many factors that might impact their health.
For example, pharma workers are exposed regularly to hazardous drugs, toxic fumes, and dangerous chemicals. Food industry workers are exposed to extreme temperatures and potentially dangerous tools and implements.
Your workers have the right to know about the potential danger of their job and the consequences that would arise from mishandling products or failing to follow instructions. Most importantly, they should be given clear direction as to how to avoid these possible dangers.
A strong safety culture includes awareness of both cause and effect, as well as consequences for those who fail to meet safety requirements. This will protect both your employees and your company.
Process safety
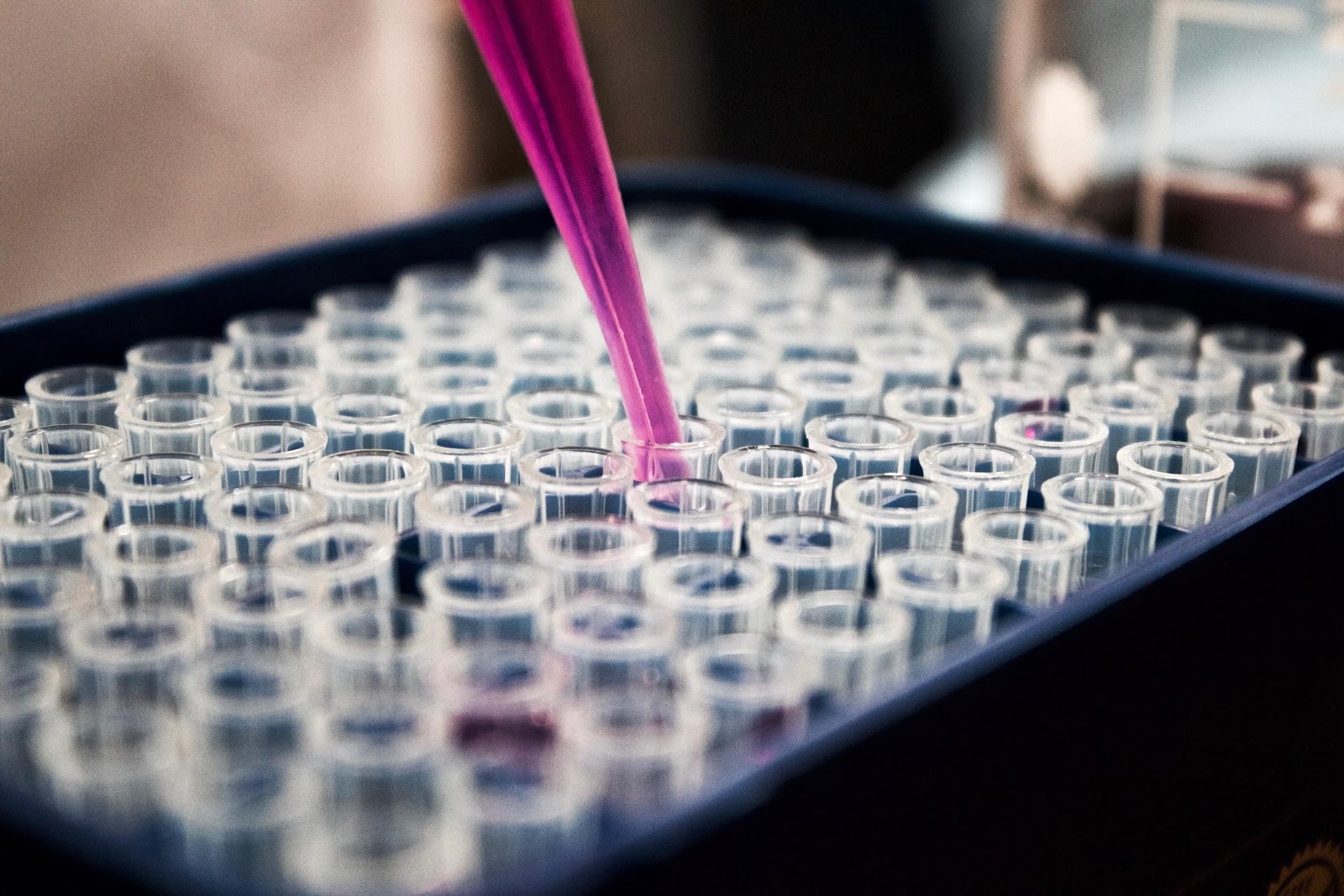
Perhaps more so than in any other industry, the actions of workers in food and pharma pose a potential impact to customer safety as much as they do to the employees themselves. To that end, sticking to appropriate work processes benefits the employee while ensuring the safety of the customer.
Your safety culture should emphasize to employees the impact of their actions on the end-user. The potential consequences of employees failing to correctly follow work processes in the food and pharma industries range from customers experiencing mild discomfort to death, something that should be taken seriously by every member of the organization.
Transportation safety
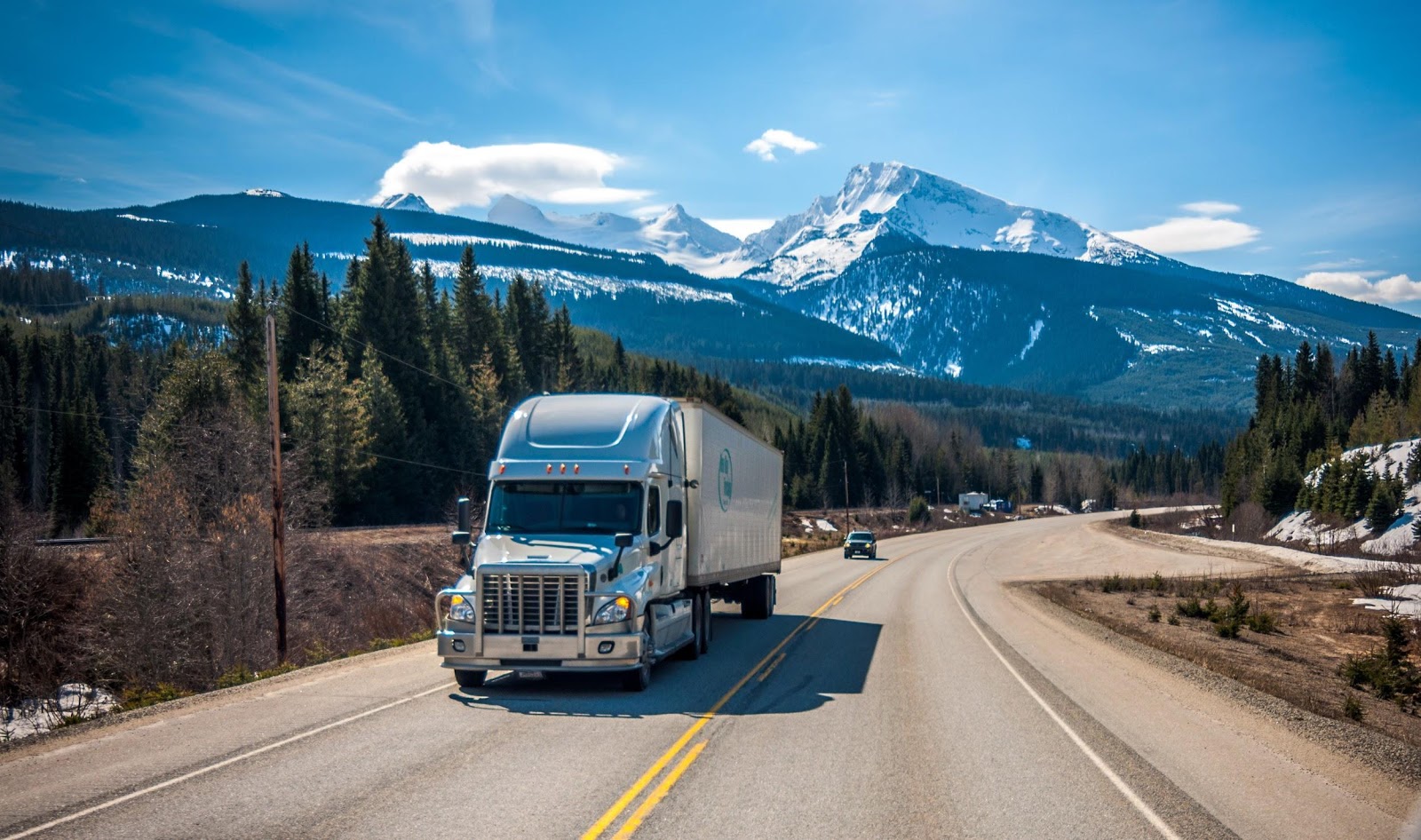
As part of the supply chain of food and pharma products, a variety of safety hazards can occur that can impact the safety of your customers as well as the reputation of your company.
Temperature-sensitive items being transported through a cold chain process must be kept at appropriate temperatures in order to avoid spoilage. Spoiled food and pharmaceuticals must be disposed of in order to avoid putting the customer at risk, which means potentially significant revenue loss.
Too humid or too dry conditions in shipping and storage can ruin a variety of items. Ensuring the right environmental conditions can avoid major losses. Further, valuable and fragile goods in transit are susceptible to shocks that can cause breakage and contamination.
Similarly, certain chemicals must be kept upright throughout shipping and storage, as tilting can cause spilling. Finally, some products can degrade when exposed to too much light or certain types of light.
Closely measuring and monitoring the circumstances of products in transit is a crucial aspect of your company’s safety culture. Data logging allows you to meet your circumstance monitoring and data collection and analysis needs in an easy manner, reducing waste and spoilage. With data logging, you can track the temperature, humidity, shock, orientation/inclination, and light exposure of your products with ease.
Plant safety
Plant safety refers to the things that all workers across every department might come into contact with on the job, including spills, maintenance, restricted areas, cleanliness, and sanitization. This type of safety is more likely to be neglected than occupational or process safety, meaning it is all the more crucial to emphasize it in your company’s safety culture.
Using a functional plant safety tracking and reporting system ensures that the process of monitoring and reporting observations and incidents in the workplace is as easy and uncomplicated as possible, meaning that no plant safety details will get lost in the mix.
Food and drug safety
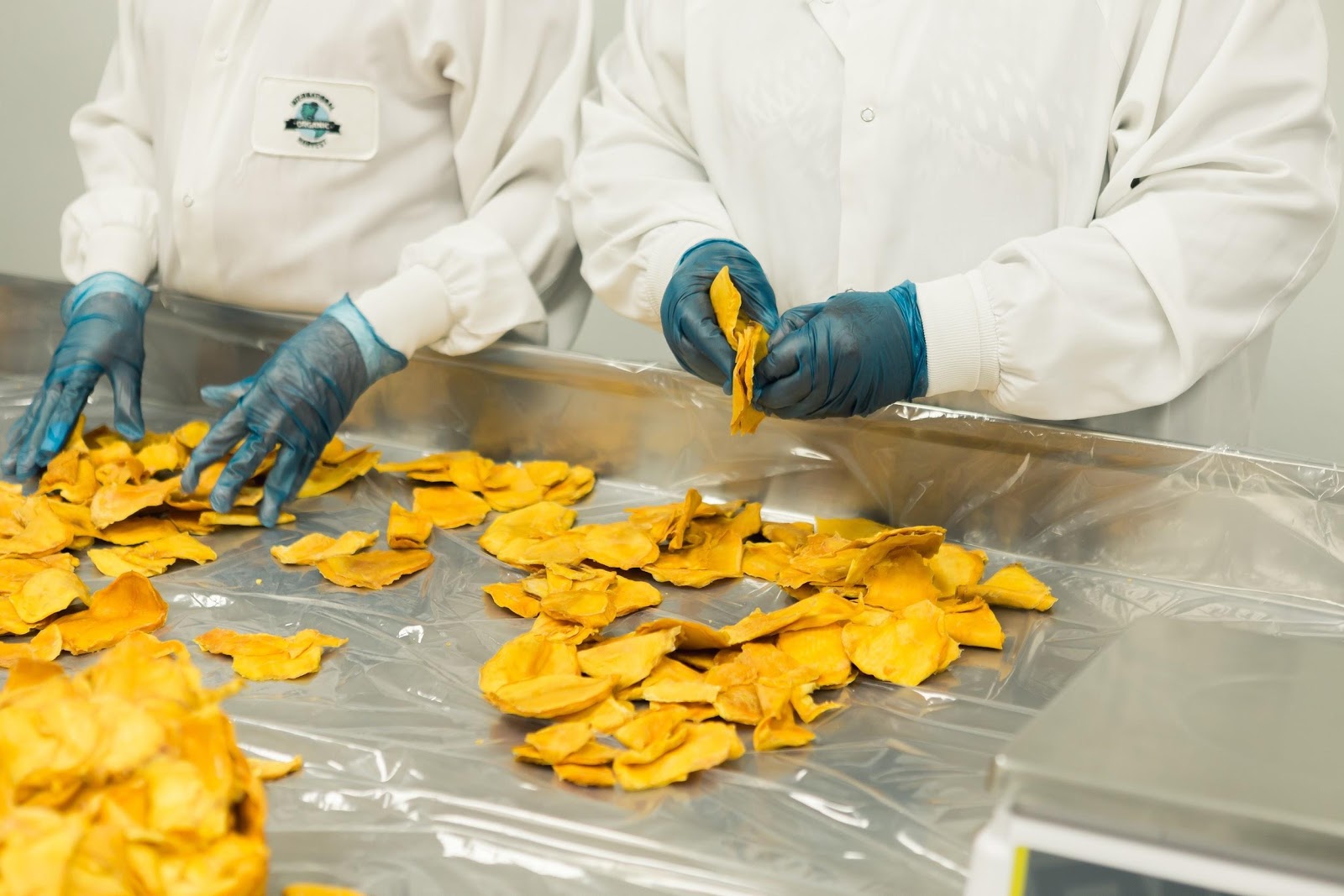
The quality of your food and pharmaceutical products, as well as their safety for consumption, is impacted by the actions of every employee at your company on a daily basis. A lapse in judgment or following procedure poses serious health risks to your customer.
To make sure each employee is up-to-date with the most recent and relevant safety procedures and knows the potentially life-or-death impact of their actions, you must provide ongoing safety training, not just as part of the onboarding process. Brief check-ins are recommended at least quarterly, and more in-depth training should be considered once a year.
In conclusion
Safety should be one of the top concerns of every member of your organization spanning the entire employee structure. The only way to assure that each and every employee is on the same page about its priority and application is to create, reinforce, and embrace a company culture of safety. This should be viewed as an ongoing process that requires participation and buy-in from top to bottom.
For more information about how data logging software can contribute to your company’s safety culture and mitigate potential risks, take a look at our customer stories and industries.